Journey of Metals: Steelmaking
Steel is part of our daily lives – from the kettles that we use to make our morning cup of tea, to the trains that take us to work. We are surrounded by steel and it has transformed our world.
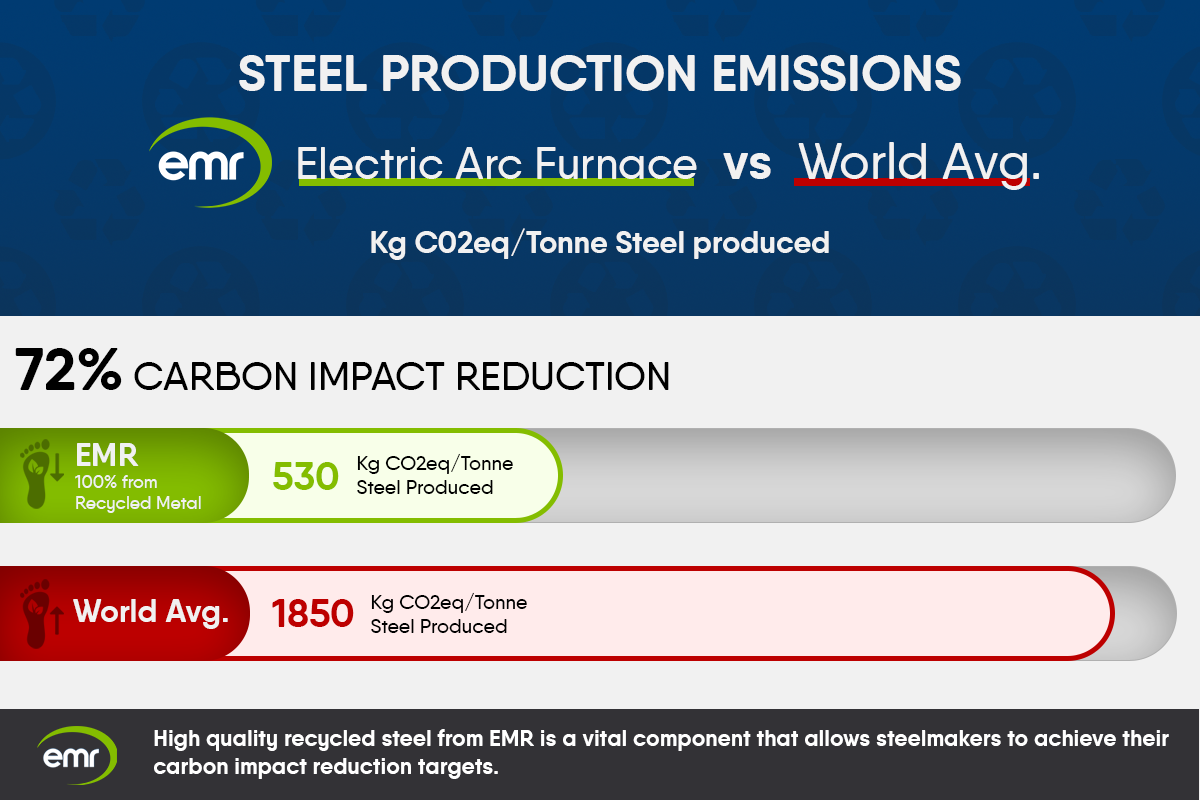
As a leading metal recycler, EMR is helping the steel industry to adapt, by providing recycled steel for the kettles and trains of the future.
Steel is an alloy, which means it requires more than one ‘ingredient’ – in this case iron and carbon. The raw materials used for steel production (iron ore and coking coal) come from mines all over the world. Extracting and transporting these raw materials emits large quantities of greenhouse gases and causes environmental destruction.
To understand these challenges, it helps to understand in more detail the way steel production works today.
Of the two main methods of steel production, the most common is currently the basic oxygen steelmaking (BOS) process, which uses iron ore from the ground to make steel in a two-stage process. The iron is first extracted from the ore at temperatures of around 2,000˚C in a blast furnace where iron ore reacts with coke (made from coal) in a reaction that produces liquid iron.
If the process stops here, it creates pig iron. Like steel, pig iron is a mixture of iron and carbon but the high carbon content means the metal can become brittle. Despite this, pig iron can still be used in some applications as cast iron (one example is engine blocks for the car industry). However, this metal wouldn’t work for a lot of the ways we use steel. For example, if the central reservation barriers on a motorway were made of pig iron they would most likely shatter on impact.
To create a metal that is fit for purpose as a structural product, the second stage, basic oxygen steelmaking (BOS), takes the liquid iron and pours it into a BOS converter where excess carbon and other impurities can be removed.
This is where a metal recycler like EMR comes in. To make the process as effective as possible, the BOS plant uses recycled scrap metal (approximately one-part recycled scrap to four parts liquid iron). Some of this recycled material is generated internally by the steel works. The rest is end of life material collected and processed by recyclers like EMR. Adding recycled scrap metal reduces the tonne for tonne carbon emissions of the final product. This is because the process of collecting and preparing recycled metals generates significantly lower carbon emissions than the processes of extracting and converting iron ore with coal.
At the next stage of the steel manufacturing process, known as secondary steel making, the amounts of other key metals in the metal are adjusted, depending on its intended use. For example, if a customer needs easily-machinable free cutting steel, adding lead can make the final steel easier to shape into nuts, bolts and household appliances. Adding nickel, molybdenum and other metals, meanwhile, can deliver improved corrosion resistance or other mechanical properties for heavy-duty uses.
One benefit of using recycled steel from EMR is we can select materials for recycling which already contain these additional metals, reducing the need for mined or ‘virgin’ materials.
The alternative process for steel making is in the Electric Arc Furnace (EAF). This method was developed in the early 20th century. It removes the need to use coke made from coal.
EAFs can use up to 100 percent recycled steel, although often they will mix recycled steel with ‘Direct Reduced Iron’, derived from iron ore.
Direct reduced iron (DRI), also called sponge iron, is produced from iron ore in a broadly similar way to the blast furnace route by reacting iron ore (in the form of lumps, pellets, or fines) directly with a special gas produced from natural gas or coal.
The steel industry is always looking to use more recycled materials from suppliers like EMR because it helps to reduce their carbon footprint. EAFs have a key role to play in this because they can melt recycled steel efficiently.
And there are other advantages. Unlike blast furnaces, EAFs can be switched on and off with relative ease, allowing for a more flexible steel industry.
Electric Arc Furnaces consume electric power, which may either be generated from fossil fuels or from renewable sources. When they use renewable power, this greatly reduces their associated carbon emissions. Even when they use power derived from fossil fuels EAF steel made from recycled scrap generates less carbon impact than steel made originally from iron ore by the Basic Oxygen Steelmaking route or from Direct Reduced Iron.
Consumers increasingly choose products that limit the carbon impact of their own lives. Manufacturers are responding to those demands. This is leading steel makers to develop new grades of low carbon impact ‘green’ steel made primarily from recycled steel.
Green steel benefits manufacturers by providing them with a way to make their products more sustainable. In the coming years consumers will be able to choose between products made with conventional ore-derived steel and those made with green steel. Unsurprisingly, we’re hearing from more and more manufacturers that want to source green steel in this environmentally conscious way.
High quality recycled steel from companies like EMR will be a vital component of the feed mix that will allow steelmakers to achieve their carbon impact reduction targets for these new grades.
There is further the industry can go. Many steel manufacturers are developing new hydrogen - based steel making routes, which will help the industry to achieve its ultimate goal of carbon-free steel production.
Steel is one material that we can never walk away from as it performs so many vital roles. By working closely with the steel industry, EMR is ensuring there is a greener, less wasteful, future for this essential metal.